Глинозём А1 2 О 3 является основным исходным материалом в производстве алюминия. Рудной базой для производства глинозёма служат преимущественно бокситы, а также нефелины, алуниты и некоторые другие глинозёмсодержащие руды.
Первая модификация - α-глинозём представляет собой безводную форму оксида алюминия с плотностью 4,0 г/см 3 эта форма глинозёма практически негигроскопична. Поверхность зёрен имеет повышенную шероховатость. Это придаёт глинозёму меньшую сыпучесть и он с трудом просыпается через отверстия; α-глинозём обладает повышенной абразивностью.
Характеристики сырья обеих провинций сходны, а преобладающий гидроксид алюминия является диаспорой, большей твердости и, следовательно, более трудным для обработки. Высокое содержание щелочей в этих сырьевых материалах по сравнению с южноамериканскими бокситами подразумевает более высокое содержание жидкой фазы при высоких температурах, что отрицательно сказывается на механических свойствах огнеупора. В Китае сырой боксит, в зависимости от провинции, можно прокаливать в разных типах печей: шахтных, круговых или вращающихся, обеспечивая продукты с различными свойствами и свойствами.
Плотность γ-глинозёма равна 3,77 г/см 3 . Эта модификация глинозёма гигроскопична, структура зёрен рыхлая. Зёрна γ-глинозёма имеют развитую поверхность и химически весьма активны. Сцепление зёрен γ-глинозёма невелико и такой глинозём отличается повышенной текучестью. По мере повышения температуры и продолжительности кальцинации зёрна γ-глинозёма уплотняются, промежутки между кристаллитами сокращаются и γ-глинозёма переходит в модификацию α- глинозёма.
Бокситы, прокаленные в шахтных и круглых печах, демонстрируют высокую гетерогенность по своим характеристикам из-за типа прокаливания. Большая однородность достигается за счет использования вращающихся печей, которые уже установлены в обеих провинциях, что значительно улучшает качество китайских бокситов.
Высокое содержание диоксида кремния присутствует в бразильском боксите, с небольшим количеством щелочи, вносит вклад в большее количество муллита, фактор, который привел к открытию огнеупорного рынка для этого бразильского продукта. Вступление китайской продукции по более низким ценам, в дополнение к другим рыночным факторам, способствовало изменению этого сценария. Сегодня на Китай приходится около 65% мирового потребления, а на Гайану приходится 20% производства, а Бразилия - на 15%.
Как выбрать необходимый для производства глинозём и правильно оценить его качество? Можно назвать несколько определяющих требований к качеству глинозёма:
Повышенная скорость растворения в электролите и достаточная адсорбционная (поглащающяя) активность поверхности относительно летучих фтористых соединений;
Хорошая текучесть при возможно меньшем пылении;
Было проведено несколько исследований между основными сырьевыми материалами каждой страны. Более высокая эффективность вращающейся печи, в случае бразильского образца, способствует снижению пористости примерно до 10% против 15% других поставщиков. Огнеупорные бокситы южноамериканского происхождения преимущественно гибситовые, обладающие поведением при явном обжиге китайского сырья, преимущественно диаспорического.
Шнайдер и Майдич изучали процессы превращения при прокаливании тугоплавких бокситов. Основная фаза, гиббсит, теряет гидроксилы в виде воды при приблизительно 350 ° С, получая метастабильные оксиды алюминия, как можно видеть на рис. Меньшая часть образовавшегося муллита обусловлена трансформациями каолинита. Присутствие этих примесей значительно уменьшает температуру плавления фазы тиалита либо его присутствием в твердом растворе, либо путем образования фаз. Эта фаза будет кристаллизоваться только при охлаждении материала, а остаточная жидкость при более низких температурах превращается в стекло.
Удовлетворительные теплофизические свойства.
В промышленных условиях следует стремиться к максимальному совмещению этих свойств в используемом глинозёме. В табл. 2.1 приводится общеизвестная классификация глинозёма по видам.
Таблица 2.1 Классификация глинозёма по физическим свойствам
Согласно этой классификации глинозёмы подразделяются на следующие типы:
Минералогически китайские бокситы можно разделить на два типа: диаспорокаолинит и диаспоро-пирофиллит. Основными кристаллическими фазами, присутствующими в необработанном образце, являются: диаспора, главным образом, и анатаза, каолинит и слюда в качестве вспомогательных минералов.
Однако образование муллита в основном нарушается ингибирующим действием щелочных оксидов из разложения слюды. Во время охлаждения материала осаждение фазы тиалита происходит между зернами оксида алюминия-альфа и образованием стекла из остаточной жидкости. Как описано ранее, южноамериканские и китайские бокситы сильно различаются по своему химическому и минералогическому составу. Некоторые систематические исследования, представленные в литературе, показывают изменение химического состава основных фаз, присутствующих после прокаливания сырого боксита: оксида алюминия, муллита, тиалита и стеклообразной фазы, в попытке описать реакции, которые происходят во время термообработки.
Мучнистый (пылевидный);
С пониженной степенью кальцинации (слабопрокалённый);
Песчаный (крупнозернистый).
Второй тип глинозёма производится для некоторых отечественных предприятий с учетом использования его в установках «сухой» очистки газа.
Скорость растворения являются наиболее значимым показателем качества глинозёма. Промышленный опыт показывает, что узкий диапазон частиц глинозёма +45-100 мкм со сдвигом крупности ближе к 100 мкм и содержание α-А1 2 О 3 не более 10% (остальное γ-А1 2 О 3) обеспечивают хорошую смачиваемость и удовлетворительную скорость растворения глинозёма в электролите.
Морфология зерен в форме игл усиливает идею образования вторичного муллита для осаждение из жидкой фазы. А иллюстрирует поведение иона железа, включенного в фазовую структуру. Большое включение титана в его кристаллическую структуру может быть связано с высокой температурой кальцинирования, что позволяет установить метастабильное равновесие иона между фазой и ее средой.
Способность муллита включать большие количества железа и титана в твердый раствор привела к углубленному изучению характеристик этой фазы. Шнайдер и Уоллебен обнаружили ясную зависимость между цветом бокситовых фрагментов и содержанием железа и титана, включенными в муллит: светло-бежевые фрагменты, содержащие низкие концентрации железа и титана, в то время как фрагменты светло-серого до темно-серого низкое содержание железа и высокое содержание титана в твердом растворе в муллите. Фрагменты с высоким содержанием железа показывают коричневую окраску.
Это достигается за счёт большого содержания в глинозёме частиц γ-А1 2 О 3 имеющих развитую ультрапористую структуру, достаточно большую удельную поверхность (более 60-80 м 2 /г), определённую методом гелиевой адсорбции или сокращенно «по БЭТ», и высокую степень насыщения структуры не скомпенсированными химическими связями. Особенно велико их химическое сродство к фтору, что и придаёт им свойства повышенной растворимости в электролите. Химическое сродство глинозёма к фтору проявляется также в эффективном улавливании фтористых соединений в сухой газоочистке.
Как можно заметить, состав фазы изменяется от фрагмента к фрагменту в одном и том же образце бокситов, все еще изменяющихся в разных областях того же фрагмента. Вероятно, это связано с суммой факторов: более высоких температур кальцинирования на поверхности заполнителя, что облегчает включение ионов в кристаллическую решетку; и процесс смешения материала, который способствует во время прокаливания периферийной реакции между фрагментами с высоким содержанием примесей и фрагментами с низким содержанием примесей.
В случае железа могут быть получены две кривые в зависимости от атмосферы прокаливания, на которую подается сырье. Более высокая растворимость иона железа указывает на большее включение в структуру муллита, препятствующее его флюсующему действию рядом с жидкой фазой. Фаза мула, присутствующая в светлых фрагментах, представляет собой размеры сети, близкие к конфигурации муллита. 3: Увеличивая содержание примесей, параметры сети расширяются и конфигурация приближается к стехиометрическому соотношению 2.
Не менее важным свойством глинозёма является его способность образовывать устойчивую корку на поверхности электролита. Мягкая, но достаточно плотная корка с хорошим сцеплением частиц образуется при использовании глинозёма с теми же характеристиками по содержанию α-А1 2 О 3 и класса менее 45 мм, которые указаны выше для песчаного глинозёма.
Применение боксита растет в огнеупорной промышленности из-за его низкой стоимости, в сочетании с высокой огнеупорностью и хорошей устойчивостью к тепловому удару. Сырые бокситы южноамериканского происхождения представляют собой основные фазы гибы, каолинита и анатаза.
Китайские образцы сырья представляют собой основные фазы: диаспор, анатаз, каолинит и слюду. Концентрация муллита небольшая из-за тормозного действия щелочных и щелочноземельных оксидов на осаждение фазы. Образование вторичного муллита в китайских бокситах подавляется двумя факторами: зерна альфа-оксида алюминия, которые высокоразвиты, имеют трудности растворения в жидкости, а наличие щелочей от разложения слюды способствует растворению муллита в фазе жидкости, предотвращающей осаждение фазы. Получение гидроксида алюминия из боксита.
Такая корка хорошо пропитывается электролитом и содержит больше глинозёма, легче поддаётся разрушению при обработке электролизёров и при ударе пробойника АПГ, чем корки, образующиеся при использовании мучнистого глинозёма. Следует также отметить, что устойчивая корка образуется при условии, когда глинозём хорошо смачивается электролитом. Мучнистый глинозём, в отличие от песчаного, смачивается значительно хуже, и корка состоит преимущественно из застывшего электролита, поверх которого находится глинозём. Прочность такой корки очень высока.
В этом эксперименте была реализована теория Байерского процесса. Из боксита, основной руды, из которой извлекается алюминий, в лаборатории был получен гидроксид алюминия. Смешивая боксит с сильным основанием и оставляя смесь при нагревании, затем фильтруя смесь и добавляя сильную кислоту к фильтрату для контроля рН смеси. Затем смесь нагревают с образованием осадка, фильтруют вскоре после нагревания, проверяют присутствие сульфата и оставляют осадок в печи в течение примерно 12 часов, после чего добавляют гидроксид алюминий.
Процесс Байера полностью не воспроизводится, поскольку он кальцинирует гидроксид алюминия, превращая его в оксид алюминия, также известный как оксид алюминия. Боксит представляет собой гетерогенный материал, состоящий в основном из одного или нескольких гидроксидов алюминия и различных смесей диоксида кремния, оксида железа, оксида титана, алюмосиликата и других примесей в незначительных количествах.
Теплопроводность и объёмная плотность глинозёма играют большую роль в тепловом балансе электролизёра, в том числе в регулировании тепловых потерь через глинозёмную засыпку или укрытие анодного массива у электролизёров ОА, в поддержании стабильного уровня электролита и защите боковых поверхностей анода от окисления.
Текучесть глинозёма определяется в основном гранулометрическим составом материала, а также содержанием в нём α-А1 2 О 3 . Материалом с хорошей текучестью можно считать глинозём с пониженной степенью прокалки. Он имеют крупность зерна более 45 мкм, высокую степень однородности гранулометрического состава и угол естественного откоса 30-40°. Однако в наибольшей степени требованию высокой текучести удовлетворяет песчаный глинозём, содержащий фракцию < 45 мкм не более 10% и α-А1 2 О 3 в пределах 5%, с углом естественного откоса менее 35°.
Боксит является наиболее широко используемым сырьем для производства глинозема в промышленных масштабах. Другие сырьевые материалы, такие как анортозит, алунит, угольные отходы и сланцевое масло, предлагают дополнительные потенциальные источники оксида алюминия. Несмотря на то, что для новых установок, использующих новые технологии, потребуются новые установки, оксид этих небукситовых материалов может удовлетворить спрос на первичный металл, огнеупоры, алюминиевые химикаты и абразивы. Синтетический мулит, полученный из кианита и силиманита, заменяет бокситовый огнеупор.
Глинозёмы со слабой текучестью и углом естественного откоса >40-45° комкуются при контакте с электролитом. Образовавшиеся комки обволакиваются электролитом и, имея больший удельный вес, оседают через границу металл-электролит, образуя осадок.
Кроме того, на электролизёрах ВТ глинозёмы с плохой текучестью при перемещении анода зависают, образуя пустоты, по которым воздух проникает до боковых граней анода и окисляет их. Однако если текучесть глинозёма будет слишком велика, то надежное укрытие анодов будет затруднено, что особенно важно для электролизёров с обожженными анодами.
Хотя более дорогие, карбид кремния и оксид алюминия-циркония заменяют бокситовые абразивы. Большая часть добычи бокситов в мире используется в качестве сырья для производства глинозема химическим каустическим выщелачиванием, известным как процесс Байера.
Оксид алюминия должен быть очищен до его очистки до металлического алюминия. Другие компоненты бокситов не растворяются и могут быть отфильтрованы в виде твердых примесей. Затем раствор гидроксида охлаждают и растворенный гидроксид алюминия осаждается в белое твердое вещество. Вакуумная фильтровальная установка.
Потери глинозема за счет уноса с анодными газами в виде пыли зависят, главным образом, от его гранулометрического состава (от содержания фракции менее 10-20 мкм), от технологии обработки электролизёров, настройки АПГ и частоты анодных эффектов. Суммарные потери мучнистого глинозёма составляют 17-25 кг/т алюминия, что на ~ 10-15 кг/т выше по сравнению с результатами для песчаного глинозёма.
После нагревания смесь подвергали вакуумной фильтрации на воронке Бюнчера, промывая твердое вещество, присутствующее в смеси, с дистиллированной водой. Возобновление процесса, предварительно сохраненную смесь нагревали в течение 10 минут. Осадок, образовавшийся во время нагревания, подвергали горячей фильтрации, испытание проводили для сульфатного иона 3 раза с хлоридом бария, и ожидается, что он будет получать самую низкую концентрацию ионов этого типа в осадке. Осадок переносили в чашку Петри и доводили до печи при температуре около 105 ° С в течение 12 часов.
В глинозёме, используемом для производства алюминия, должно содержаться минимальное количество соединений железа, кремния, тяжелых металлов с меньшим потенциалом выделения на катоде, чем алюминий, т.к. они легко восстанавливаются и переходят в катодный алюминий. Нежелательно также присутствие в глинозёме избытка оксидов щелочных металлов, поскольку они вступают во взаимодействие с фтористым алюминием электролита по реакции, разлагают его и тем самым нарушают установленное криолитовое отношение. Для восстановления к.о. требуется корректировка электролита фтористым алюминием, что удорожает стоимость первичного алюминия. В случае содержания Na 2 О в глинозёме 0,3 % и более при работе на кислых электролитах начинается наработка излишнего количество электролита, который необходимо периодически сливать из ванны.
Реакция выражается следующим образом. Алюминат калия растворяется в воде, образуя основную среду, которая заставляет примеси осаждаться, так как они нерастворимы в такой среде, образуя грязь окраски, очень похожую на глину. Эта реакция вызывает нейтрализацию среды, о чем свидетельствует тест на голубой бульон, этот индикатор показывает желтый цвет, когда кислотный, синий, когда основной и зеленый, когда нейтральный.
Нагревание смеси осаждалось из ранее образовавшегося гидроксида алюминия. Система отфильтровывалась в горячем виде для отделения осадка от водной фазы. Полученная соль нерастворима, делая образец облачным. Можно сделать вывод, что процесс Байера был воспроизведен как на практике, так и в литературе, благодаря чему гидроксид алюминия можно успешно получить в качестве конечного продукта. Также делается вывод о том, что процесс не был полностью воспроизведен, поскольку его основная цель - производство оксида алюминия, оксида алюминия, и это получается из гидроксида алюминия при прокаливании при высокой температуре.
Для расчёта количества A1F 3 {Сфа, кг), требуемого для корректировки электролита, можно пользоваться формулой И.П. Гупало
Сфа = 2т (K1 - К2) / С (2 + K1)K2
где: K1 и К2 - к.о. электролита соответственно до и после корректировки; т - масса корректируемого электролита, кг; С - содержание A1F 3 в промышленной соли фтористого алюминия, доли ед.
В: Химия в повседневном подходе. Сан-Паулу: Модерна, стр. 128. В: География для средней школы. Общая география и Бразилия. 1-е изд. Сан-Паулу: Сципион, стр.: 465. Его промышленное производство начинается чуть более века назад. Сразу после того, как Карл Йозеф Байер запатентовал свою технику, чтобы превратить боксит в глинозем.
Только 89 присутствуют в природе, главным образом в виде соединений и редко в виде чистых элементов. Другие 20 элементов, которые занимают нижнюю часть Периодической таблицы, были обнаружены во время исследований атомной энергии. В ожидании составления учебника по химии для своих учеников Менделеев думал о классификации элементов по их химическим свойствам, согласно схеме. Это показывает периодичность химических свойств элементов, классифицированных по их атомному весу. Его теории восторжествовали, когда были обнаружены три элемента, из которых он ожидал существования.
Эта формула с соответствующими коэффициентами на состав сырья, срок службы электролизёра, температуру электролита и др. служит основой существующих методик расчета корректирующей дозы фтористого алюминия.
Пример. Примем в формуле И.П. Гупало m = 10 000кг, С = 0,9, исходное к.о. 2,4, целевое к.о. 2,35. Для корректировки потребуется 106 кг фтористого алюминия.
На основании изложенного материала можно считать, что
весьма приемлемыми свойствами обладает глинозём следующей спецификации:
Гранулометрический состав по фракциям, %
100 + 45 мкм, не менее 85
45 мкм, не более 10
Угол естественного откоса, град, не более 35
Удельная поверхность по БЭТ, м 2 /г, не менее 60
Потери при прокаливании, %, не более 0,8
По химическому составу глинозём должен соответствовать требованиям, приведенным в ГОСТ 30558-98 «Глинозём металлургический» (табл. 2.2).
Таблица 2.2 Требования к глинозёму
Примечания: 1. Тяжелые примеси - сумма оксидов Ti0+V 2 0 5 +Cr 2 0 5 +Mn0.
2. П.п.п. - потери при прокаливании, имеющие физический смысл контроля остаточных летучих веществ после кальцинации.
КОНСТРУКЦИЯ АЛЮМИНИЕВЫХ ЭЛЕКТРОЛИЗЕРОВ, ИХ МОНТАЖ И ДЕМОНТАЖ
Общая характеристика и классификация электролизеров
На предприятиях алюминиевой промышленности эксплуатируются электролизеры весьма разнообразных конструкций и мощности. Условно их разделяют на три большие группы:
Электролизеры малой мощности иа силу тока до 100 кА. Этот тип ванн оснащен одним самообжигающимся анодом с боковым подводом тока (БТ) и одноэтажным (напольным) размещением в корпусе (рис. 3.1). Это наиболее старые с конструктивной точки зрения электролизеры и доля их в мировом производстве алюминия невелика (по РФ около 15%).
Электролизеры средней мощности на силу тока 100-165 кА, оснащенные также одним самообжигающимся анодом с верхним подводом тока (ВТ) и преимущественно с размещением на отметке + 4,0 м. Этот тип ванн (рис. 3.2) осваивался в нашей стране в 60-70-е годы и на его долю в РФ приходится большая часть производственных мощностей (около 70%).
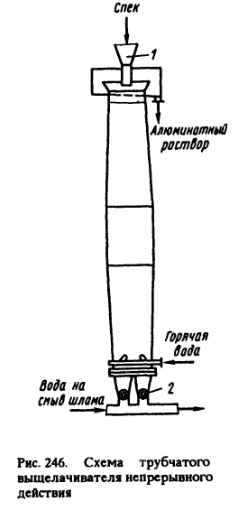
Электролизеры средней и большой мощности на силу тока от 160 до 400 кА и более, оснащенные предварительно обожженными анодами (ОА) (рис. 3.3). Количество анодов на электролизере зависит от его мощности. Размещение ванн преимущественно на отметке + 4,0 м. Это наиболее современный тип электролизеров, хотя именно с такого типа ванн небольших размеров начиналась история развития алюминиевой промышленности.
Рис. 3.3. Алюминиевый электролизер с предварительно обожженнымианодами: а-схематическое изображение; б-поперечный разрез электролизера; в- корпус электролиза с поперечным расположением электролизёров на силу тока 180 кА (VAW, Германия)
В чем преимущества или недостатки того или иного типа электролизеров? Первые два из них, оснащенные самообжигающимися анодами, отличаются простотой конструкции и возможностью использовать для формования анода относительно дешевый материал - анодную массу. Использование для обжига тепла выделяющегося в электролизере. Отсутствуют какие-либо отходы от использования анодов в электролизном производстве. Не требуется больших инвестиций в производство анодной массы. Затраты на производство единицы продукции на электролизерах этого типа существенно ниже.
Недостаток электролизеров с самообжигающимися анодами состоит в том, что на них ограничены возможности повышения единичной мощности ванн, а также весьма затруднено использование средств механизации и автоматизации, в том числе систем автоматизированного питания глиноземом (АПГ). В электролитический алюминий поступает значительное количество железа из-за коррозии стальных штырей и газосборных секций, что ограничивает возможность получать алюминий высших сортов (особенно на электролизёрах ВТ). При обжиге анодов в атмосферу попадает значительное количество вредных для здоровья углеводородов - смол и газов. Кроме того система газо и пыле улавливания работает не эффективно из за мене удачной конструкции анодного узла.
Что касается третьего типа электролизеров (ОА), то они лишены этих недостатков. На этом типе электролизера возможно повышение мощности путём увеличения числа анодов и расширения геометрических размеров ванн. Электролизёр ОА более приспособлен для механизации и автоматизации технологических операций, а сбор и очистка анодных газов производятся с большей эффективностью, в газах нет смолистых веществ и углеводородов. На этом типе ванн больше возможностей получить алюминий высших сортов, в том числе марки А8.
В настоящее время все вновь строящиеся алюминиевые заводы оснащаются электролизёрами ОА на силу тока 275-350 кА. На электролизёрах этого типа при анодной плотности тока 0,85-0,88 А/см 2 достигнут выход по току ~ 95%, удельный расход электроэнергии -13,3 кВт*ч/т А1, расход анодов 515/415 кг (брутто/нетто).
Фирма Alcan (Канада) планирует строительство опытного завода в Jonquiere с электролизёрами АР50 мощностью 500 кА. В настоящее время нет технических ограничений для создания ещё более мощного электролизёра. Например, моделирование МГД, термоэлектрических и механических параметров показывает, что электролизёры ОА могут работать при силе тока 740 кА и выше (A.Tabertaux).
В то же время себестоимость алюминия на электролизерах этого типа за счет больших инвестиционных затрат и высокой стоимости обожженных анодов на 10-15% выше. Другой проблемой можно считать образование анодных огарков, которые составляют 16-20% от массы анодов и требуют специальной обработки и утилизации в анодном производстве.
Постоянная модернизация и совершенствование конструкции позволяет успешно эксплуатировать все три типа электролизеров с использованием преимуществ каждого из них.
Как видно на рис. 3.1-3.3, на которых показаны основные типы электролизеров, принципиально алюминиевый электролизер любой конструкции состоит из катодного и анодного устройств, ошиновки (анодной и катодной) и вспомогательных конструкций, удерживающих или перемещающих отдельные узлы, а также устройств для сбора и отвода анодных газов (колокол, горелки, укрытия, балка-коллектор). Рассмотрим более детально конструктивные особенности основных типов электролизеров.
Технология производства алюминия состоит из двух стадий: первая - производства глинозема и вторая - электролитическое получение алюминия из глинозема. За рубежом практически весь глинозем получают из бокситов в основном способом Байера (К.И.Байер - австрийский инженер, работавший в России), на отечественных заводах глинозем получают из бокситов способом Байера и из бокситов и нефелинов способом спекания. Оба эти способа относятся к щелочным методам выделения глинозема из руд. Способ Байера экономически целесообразно использовать для переработки бокситов с небольшим содержанием SiO 2 (с кремниевым модулем Al 2 O 3 /SiO 2 более 5-7), поскольку при росте количества SiO 2 все больше Al 2 O 3 и используемой в процессе щелочи теряются из-за образования химического соединения Na 2 O Al 2 O 3 2SiO 2 2H 2 O.
Для переработки бокситов с кремниевым модулем менее 5-7 более экономичным является способ спекания. В связи с истощением богатых глиноземом месторождений боксита и вовлечением в производство более бедных бокситов, доля способа Байера в производстве глинозема снижается и возрастает доля способа спекания.
Способ Байера
Способ Байера - способ выделения глинозема из боксита - основан на выщелачивании, цель которого растворить содержащийся в боксите оксид алюминия Al 2 O 3 , избежав перевода в раствор остальных составляющих боксита (SiO 2 , Fe 2 O 3 и др.). В основе способа лежит обратимая химическая реакция:
Al 2 O 3 n H 2 O + 2NaOH = Na 2 O Al 2 O 3 + (n + 1)H 2 O.
При протекании реакции вправо глинозем в виде алюмината натрия переходит в раствор, а при обратном течении реакции образующийся гидратированный Al 2 O 3 выпадает в осадок. Упрощендая схема производства глинозема по способу Байера показана на рис. 244. Ниже описаны основные операции этого способа.
1. Подготовка боксита к выщелачиванию . Боксит дробят и размалывают до фракций размером 0,05-0,15 мм в среде добавляемой щелочи и оборотного раствора щелочи NaОН, добавляют также немного извести, активизирующей выщелачивание.
2. Выщелачивание . Полученную при помоле пульпу направляют на выщелачивание. Для полного протекания приведенной выше реакции вправо (образования алюмината натрия) необходимы щелочная среда, высокое давление (~ 3 МПа), нагрев пульпы до 100-240 °С (в зависимости от сорта боксита) и ее длительное (около 2 ч) перемешивание. Такие условия обеспечиваются в автоклавах - сосудах, работающих под давлением. Применяемые автоклавы представляют собой (рис.245) стальной цилиндрический сосуд диаметром 1,6-2,5 и высотой 13,5-17,5 м. Давление в автоклаве 2,5-3,3 МПа, пульпу подают сверху, снизу через патрубок 2 с барботером 3 - пар, который нагревает и перемешивает ее. Из автоклава пульпа выдавливается через трубу 1.
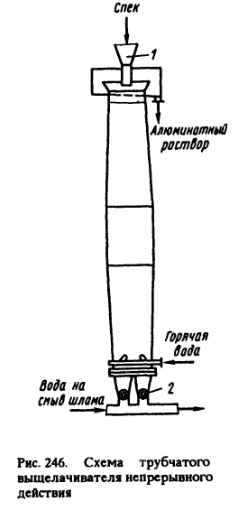
Пульпу обычно пропускают через батарею из 6-10 последовательно установленных автоклавов, где в течение ~ 2 ч содержащийся в пульпе в виде Al 2 O 3 Н 2 O, Al 2 O 3 3Н 2 O и Al 2 O 3 глинозем реагирует со щелочью (реакция приведена выше), переходя в Na 2 O Al 2 O 3 . В первый автоклав пульпу подают насосом, предварительно подогрев до ~ 150 °С, из последнего автоклава пульпа попадает в два автоклава-испарителя, в которых давление снижается до атмосферного. Продуктом является автоклавная пульпа, состоящая из алюми- натного раствора (содержащего Na 2 O Al 2 O 3) и шлама (осадка, в который выпадают остальные примеси боксита).
3. Разделение алюминатного раствора и шлама после разбавления пульпы водой производят в сгустителях (отстойниках) - сосудах диаметром 15-50 м, на дне которых оседает шлам, а через верх сливается отстоявшийся алюминатный раствор. Его дополнительно пропускают через фильтры и направляют на следующую операцию - декомпозицию. Получаемый красный шлам (окраску ему придают частицы Fe 2 O 3) идет в отвал, шлам содержит, %: Al 2 O 3 12-18, SiO 2 6-11, Fe 2 O 3 44-50, CaO 8-13.
4. Разложение алюминатного раствора , называемое также декомпозицией или выкручиванием проводят с целью перевести алюминий из «раствора в осадок в виде Al 2 O 3 3Н 2 O, для чего обеспечивают течение приведенной выше реакции выщелачивания влево, в сторону образования Al 2 O 3 3Н 2 O. Чтобы указанная реакция шла влево, необходимо понизить давление (до атмосферного), разбавить и охладить раствор, ввести в него затравки (мелкие кристаллы гидрооксида алюминия) и пульпу для получения достаточно крупных кристаллов Al 2 O 3 3Н 2 O перемешивать в течение 50-90 ч.
Этот процесс осуществляют в серии установленных последовательно и соединенных перепускными сифонами декомпозеров, через которые последовательно проходит пульпа (алюминатный раствор с выпадающими кристаллами гидрооксида алюминия). В серии устанавливают 10-11 декомпозеров с механическим перемешиванием или 16-28 декомпозеров с воздушным перемешиванием пульпы. Первые представляют собой баки диаметром до 8 м, в которых перемешивание осуществляют вращением вокруг вертикальной оси волокуш (гребков). Декомпозеры второго типа, преимущественно применяемые в настоящее время, представляют собой цилиндрические баки высотой 25-35 м и объемом до 3000 м3; снизу в них подают сжатый воздух, перемешивающих пульпу.
5. Отделение кристаллов гидрооксида алюминия от раствора и классификация кристаллов по крупности . После декомпозиции пульпа поступает в сгустители, где гидрооксид отделяют от раствора. Полученный гидрооксид в гидросепараторах разделяют на фракцию с размером частиц 40-100 мкм и мелкую фракцию (размером < 40 мкм), которую используют в качестве затравки при декомпозиции. Крупную фракцию промывают, фильтруют и направляют на кальцинацию.
6. Кальцинацию или обезвоживание гидрооксида алюминия осуществляют в футерованных шамотом трубчатых вращающихся печах диаметром 2,5-5 и длиной 35-110 м, отапливаемых природным газом или мазутом. Гидрооксид медленно перемещается вдоль вращающегося барабана навстречу потоку горячих газов, температура которых повышается от 200-300 °С в месте загрузки до ~ 1200 °С вблизи горелки у разгрузочного торца барабана. При нагреве гидрооксида идет реакция: Al 2 O 3 3H 2 O = Al 2 O 3 + 3Н 2 O, заканчивающаяся при 900 °С. Продуктом является глинозем Al 2 O 3 (порошок белого цвета).
Извлечение глинозема при использовании описанного способа Байера составляет около 87 %. На производство 1 т глинозема расходуют 2,0-2,5 т боксита, 70-90 кг NaOH, около 120 кг извести, 7-9 т пара, 160-180 кг мазута (в пересчете на условное топливо) и около 280 кВт ч электроэнергии.
Способ спекания
Способ применяют для получения глинозема из высококремнистых (> 6-8 % SiO 2) бокситов с кремниевым модулем менее 5-7 и из нефелиновых руд; способ пригоден также для переработки любого алюминиевого сырья.
Сущность способа заключается в получении твердых алюминатов путем их спекания при высоких (~ 1300 °С) температурах и в последующем выщелачивании полученного спека.
Получение глинозема из бокситов
Основные стадии этого процесса следующие.
Подготовка к спеканию . Боксит и известняк после дробления измельчают в мельницах в среде оборотного содового раствора с добавкой свежей соды Na 2 CO 3 , получая пульпу с влажностью 40 %.
Спекание ведут в отапливаемых трубчатых вращающихся печах диаметром до 5 и длиной до 185 м. Температура в печи повышается от 200-300 °С в месте подачи пульпы до ~ 1300 °С в разгрузочном конце у горелки. При нагреве оксид алюминия превращается в водорастворимый алюминат натрия:
Al 2 O 3 + Na 2 CO 3 = Na 2 O Al 2 O 3 + CO,
а кремнезем связывается в малорастворимые силикаты: SiO 2 + 2СаО = 2СаО Si02. С содой реагирует также Fe 2 O 3 боксита, образуя NaaO Fe203. Эти химические соединения спекаются, образуя частично оплавленные куски - спек.
После обжиговой печи спек охлаждают в холодильниках, дробят до крупности 6-8 мм и направляют на выщелачивание.
Выщелачивание ведут горячей водой проточным методом в аппаратах различной конструкции: диффузорах (цилиндрических сосудах, куда порциями загружают и выгружают спек), в конвейерных выщелачивателях и др. Наиболее совершенными являются трубчатые выщелачиватели непрерывного действия (рис. 246). Загружаемый через бункер 1 в сосуд высотой 26 м спек благодаря непрерывной выгрузке секторными разгружателями 2 движется вниз и промывается встречным потоком воды. В воде растворяется алюминат натрия, вода разлагает также феррит натрия Na 2 O Fe 2 O 3 и Fe 2 O 3 выпадает в осадок. Продуктами выщелачивания являются алюминатный раствор и красный шлам, содержащий Fe 2 O 3 , Al 2 O 3 , SiO 2 , CaO. В алюминатный раствор переходит немного кремнезема в виде гидросиликатов, в связи с чем раствор подвергают обескремниванию.
Обескремнивание алюминатного раствора осуществляет в батарее автоклавов длительной (~ 2,5 ч) выдержкой при температуре 150-170 °С. В этих условиях вырастают кристаллы нерастворимого в воде соединения Na 2 O Al 2 O 3 2SiO 2 2Н 2 О (иногда к раствору добавляют известь, в этом случае образуются кристаллы СаО Al 2 O 3 2SiO 2 2H 2 O). Из автоклавов выходит пульпа, состоящая из алюминатного раствора и осадка - белого шлама. Далее раствор отделяют от белого шлама путем сгущения и фильтрации. Белый шлам идет в шихту для спекания, а раствор направляют на карбонизацию.
Карбонизацию проводят с целью выделения алюминия в осадок Al 2 O 3 3Н 2 O (карбонизация заменяет декомпозицию в способе Байера). Карбонизацию осуществляют в сосудах цилиндрической или цилиндроконической формы объемом до 800 м 3 пропусканием через раствор отходящих газов спекательных печей, содержащих 10-14 % СO 2 . Газы перемешивают раствор, а СO 2 разлагает алюминат натрия: Na 2 O Al 2 O 3 + СO 2 + 3Н 2 O = Al 2 O 3 3Н 2 O + Na 2 CO 3 и гидроксид алюминия выпадает в осадок.
Далее проводят те же технологические операции, что и в способе Байера: отделение Al 2 O 3 3Н 2 O от раствора и кальцинацию - обезвоживание гидроксида алюминия прокаливанием в трубчатых печах с получением глинозема Al 2 O 3 .
Примерный расход материалов на получение 1 т глинозема, т: боксита 3,2-3,6; известняка 1,35; извести 0,025; кальцинированной соды 0,19; условного топлива 1,1-1,2; электроэнергии ~ 800 кВт т.
Получение глинозема из нефелинов
Нефелиновый концентрат или руду и известняк после дробления размалывают в водной среде, получая пульпу для спекания. В связи с наличием в составе нефелина щелочей не требуется добавок в шихту соды.
Спекание производят в отапливаемых трубчатых вращающихся печах диаметром 3-5 и длинрй до 190 м; пульпу заливают в печь со стороны выхода газов, где температура равна 200-300 °С, а в разгрузочном конце она достигает 1300 °С. В процессе нагрева нефелин взаимодействует с известняком:
(Na, К) 2 O Al 2 O 3 2SiO 2 + 4СаСО 3 = (Na, К) 2 O Al 2 O 3 + 2(2СаО SiO 2) + 4СO 2 .
В результате этой реакции входящие в состав нефелина Na 2 O и К 2 O обеспечивают перевод глинозема в водорастворимые алюминаты, а СаО связывает кремнезем в малорастворимый двухкальциевый силикат. Получаемый спек охлаждают в холодильниках и дробят.
Выщелачивание нефелинового спека совмещают с его размолом и проводят в шаровых или стержневых мельницах в среде горячей воды со щелочным раствором, получаемым после карбонизации. В процессе выщелачивания алюминаты растворяются в воде и остается известково-кремнистый шлам (называемый белитовым), который идет на производство цемента.
Обескремнивание алюминатного раствора проходит в две стадии. Первую проводят в автоклавах в течение 1,5-2 ч при температуре 150-170 °С; при этом в осадок выпадают содержащие кремнезем алюмосиликаты, этот осадок (белый шлам) идет в шихту для спекания.
Алюминатный раствор после первой стадии обескремнивания делят на две части. Одну часть далее подвергают карбонизации (так, как при переработке бокситов) с последующей декомпозицией, после чего получают в осадке гидрооксид алюмния и содощелочной раствор, идущий на выщелачивание спека.
Вторую часть алюминатного раствора дополнительно обескремнивают в мешалках с добавкой извести при ~ 95 °С в течение 1,5-2 ч. При этом в осадок выпадает известковосиликатный шлам и обеспечивается глубокое обескремнивание алюминатного раствора. Затем этот раствор подвергают кальцинации, получая в осадке гидроксид алюминия и глубоко обескремненный содовый раствор, из которого далее в содовом цехе получают поташ (К 2 СО 3) и кальцинированную соду (Na 2 СO 3); глубокое обескремнивание необходимо для получения этих товарных продуктов.
Кальцинация . Гидрооксид алюминия после обеих ветвей переработки алюминатного раствора подвергают промывке и фильтрации и затем направляют на кальцинацию (обезвоживание), которую проводят так же, как в способе Байера, получая глинозем.
Примерный расход материалов на получение 1 т глинозема из нефелинов, т: нефелина 4; известняка 7; извести 0,1; условного топлива 1,5; электроэнергии ~ 1000 кВт ч. При этом получают около 1 т содопродуктов и до 10 т цемента.