Зубья колес нарезают на фрезерных или специальных зуборезных станках.
Существует два основных способа нарезания зубьев: 1) копирование, осуществляемое на фрезерных станках с помощью дисковой (рис. 9, а) или пальцевой (рис. 9, б) фрез, режущие кромки которых имеют профиль, соответствующий профилю впадин зуба; 2) обкатка, осуществляемая на зубофрезерных или зубострогальных станках с помощью соответствующего режущего инструмента - червячной фрезы (рис. 10, а), долбяка (рис. 10,6), инструментальной рейки-гребенки (рис. 10, в), находящихся в непрерывном зацеплении с заготовкой на всей стадии нарезания зубьев. Способ обкатки обеспечивает высокую производительность и достаточную точность изготовления зубчатых колес.
Зубчатое колесо и инструмент получают относительное движение с помощью удобного механизма, как если бы имели место примитивные периферии. Инструмент также имеет переменное движение в направлении своей оси, необходимое для удаления чипа. Очевидно, что у него есть инструмент для каждого значения модуля. В других машинах примитивная периферия колеса, подлежащего разрезанию, рулонах на примитивной плоскости зубного протеза, которая может принимать только альтернативное движение работы, чтобы удалить чип; используя профилирование для разработчика, профиль протеза, а затем режущую кромку инструмента, который воспроизводит его, является прямым и может быть легко достигнут с максимальной точностью.
В последнее время в массовое производство внедряют метод; горячей накатки зубьев, который производится на специальном зубонакатном станке, состоящем из двух валов, жестко связанных между собой делительной передачей. На один из валов насаживают вальцевальное зубчатое колесо, а на другой - нагретую до температуры ковки заготовку. Валы перемещаются друг к другу под большим давлением; при этом вальцевальное колесо накатывает зубья на заготовке.
Те же самые машины, описанные здесь, поддаются некоторым вариантам выполнения цилиндрических зубчатых колес со спиральными зубцами. В этих инструментах, состоящих из винтовой фрезы, режущие кромки которой представляют собой линии, лежащие на развивающемся геликоиде, вращается вокруг своей оси с равномерным движением, медленно двигаясь в направлении оси рабочего колеса: последний Регулируя скорость вращения колеса по отношению к инструменту и соответствующим образом регулируя ось бурового долота, колесо обрезается прямыми или винтовыми зубьями и, учитывая определение колеса режущие кромки, профилирование развивается.
При массовом (крупносерийном) изготовлении зубчатых колес горячая накатка дает существенную экономию по сравнению с ранее рассмотренными методами нарезания зубьев. Недостаток - меньшая точность накатанных зубьев по сравнению с нарезанными.
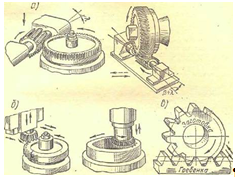
После нарезания зубья могут быть подвергнуты окончательной обработке: шлифованию, шевингованию или притирке, обеспечивающим необходимые точность и шероховатость рабочих поверхностей зубьев.
Эта система позволяет не только исключить использование делителя, но и непрерывно разрезать зуб во время движения поколений. С подобной системой вырезаются колеса для колесных пар и вечная жизнь. Режущие кромки спирального резака соответствуют сечениям резьбовой резьбы, и, когда фрезерный станок вращается вокруг своей оси, колесо вращается вокруг перпендикулярной оси, как если бы он приводился в движение винтом, а его зубы были обрезаны оболочкой. Принцип, на котором основана система режущей огибающей, также используется при выполнении конических зубчатых колес.
Заготовки для изготовления зубчатых колес могут быть получены литьем, ковкой (штамповкой).
Зубчатые колеса изготовляют из углеродистой стали (Ст5, Ст6, сталь 35; 45; 50; 50Г и др.), легированной стали (12ХНЗ; 15Х; 20Х; 35Х и др.), стального литья (35Л; 45Л; 55Л и др.), чугуна (СЧ 15 - 32; СЧ 18-36; СЧ 21-40 и др.), неметаллических материалов (текстолит, капрон, ДСП и т. п.) (см. табл. ПЗ, П21,П28).
В качестве колеса ассортимента необходимо сначала определить форму зуба колеса серии, из которого будут получены все остальные профили путем обволакивания. Как правило, он начинается с определения зуба плоского колеса, и этот зуб ограничивается прямыми плоскими зубчатыми зубьями для необходимости получать на разных участках зубообразующих гомотетических профилей с одной режущей кромкой. Различные типы используемых машин отличаются тем, как можно отрезать относительное движение конического колеса по сравнению с плоским колесом, зуб которого представлен инструментом.
Чугунные зубчатые колеса применяют в тихоходных передачах. Зубчатые колеса из неметаллических материалов работают в паре с металлическими и применяются для понижения шума быстроходных передач небольших мощностей.
К материалам, применяемым для изготовления зубчатых колес, предъявляют требования достаточной общей и поверхностной прочности, выносливости зубьев при изгибе, стойкости против абразивного износа заедания. Указанным требованиям лучше, всего удовлетворяют термически или термохимически обработанные стали.
Инструмент затем принимает рабочее движение, как в извести, аналогично тому, что было видно для многих описанных выше передач. Таким образом, на машине Глисона плоское колесо и режущее колесо вращаются вокруг неподвижных осей в пространстве и конкурируют в точке, а закон движения идентичен тому, что произойдет, если примитивная поверхность должна быть проведена. Поверхности отдельных зубов полностью разрезаются, и когда один из них закончен, машина возвращается в исходное положение, а делитель продвигает колесо на один шаг.
Однако в машине Бильграма инструмент имеет единственную альтернативную работу, в то время как шестерня движется так, как если бы ее примитивная поверхность перевернулась до соответствующей фиксированной плоской колесики в пространстве. В этой передаче после каждого хода инструмента делитель продвигает колесо на один шаг; таким образом, все зубы частично обрабатываются и в данный момент находятся на одной и той же стадии обработки; это позволяет избежать возврата машины в исходное положение для каждого зуба, как на машине Глисона.
Нормализация--нагрев материала до температуры, незначительно "щей температуру верхней критической точки стали, выдержка и постепенна охлаждение на воздухе или вместе с печью. Нормализации подвергают качественные углеродистые и легированные стали, а также заготовки из стального Она снимает литейные напряжения и наклеп (после ковки или штамповки) и обеспечивает получение равномерной структуры материала по всему объему заготовки.
Некоторые современные машины, предназначенные для резки, всегда для обволакивания, зубы, определенные особыми формами зуба протеза или плоского колеса, особенно интересны для их производства и производства. Машина фирмы Глисон производит конусообразную коническую шестерню, соответствующую плоскому колесу с зубцами, образованными круговой прямоугольной конической поверхностью с нормальной осью на примитивной плоскости самого колеса.
Инструмент, используемый в машине, представляет собой зубчатый резак с прямолинейными режущими кромками и расположен в соответствии с генераторами конуса, определяющими зуб плоского колеса. Резак вращается вокруг своей оси и затягивается во вращательное движение плоского сопряженного колеса с режущим коническим колесом. Режущие кромки мельницы вырезают по их движению зуб плоского колеса и относительное движение относительно рабочего колеса, а также зубцы последнего, которые разрезаются. После резки зуба машина возобновляет примитивное положение, разделитель позволяет подавать разрезанное колесо на один шаг, и цикл возобновляется. но отказ от точности формы, две смежные грани могут быть разрезаны одновременно.
Закалка (объемная и поверхностная) создает высокую твердость и прочность материала. Существенным недостатком объемной закалки является то, что подвергнутый ей материал не сохраняет вязкой сердцевины. В результате поверхностной закалки (для зубчатых колес малых и средних размеров - токами высокой частоты (ТВЧ), для зубчатых колес крупных размеров - в ацетиленовом пламени) сохраняется вязкая сердцевина при высокой твердости и прочности поверхности слоев материала. Закалке подвергают качественные углеродистые или легированные стали. Углеродистые стали обыкновенного качества не закаливают.
Если, кроме машин, которые используют винтовые лопасти, все, описанные выше, имеют, как мы видели, прерывистую операцию. Преимущество в том, что, особенно с точки зрения точности и производства, можно добиться непрерывного прогресса. Сначала поверхность лица всех зубов зубного протеза или плоского колеса образована частями одной полосатой поверхности, генераторы которой образуют постоянный угол с примитивной плоскостью и генерируется режущим инструментом прямой, который принимает подходящее параллельное движение на той же примитивной плоскости.
Улучшение - закалка с последующим высокотемпературным отпуском. Нормализованные и улучшаемые стали (качественные углеродистые и легирован! обычно применяют для изготовления зубчатых колес индивидуального или мелкосерийного производства. Они хорошо поддаются чистовой обработке и хорошо прирабатываются.
Цементация - насыщение поверхностного слоя углеродом и закалка. Цементация существенно повышает твердость и несущую способность поверхности слоя зубьев, обеспечивает высокую прочность на изгиб. Цементации обычно подвергают низкоуглеродистые стали: хромистые (15Х,20Х), хромоникелевые (12ХН3А, 18Х2Н4МА, 20Х2Н4А) для ответственных зубчатых колес, работающих с перегрузками или ударными нагрузками, и безникелевые (18ХГТ, 25ХГТ, 15ХФ).
Движение инструмента для создания поверхности зуба протеза или плоского колеса можно рассматривать как результат двух плоских движений, всегда параллельных примитивной поверхности: первый описывает точки инструмента замкнутой траектории соответствующей формы с установленным законом; второй состоит из равномерного переноса в случае протеза или вращения, хотя он равномерен вокруг оси в случае плоского колеса.
В практическом варианте осуществления инструмент описывает только замкнутую траекторию, и колесо, которое нужно отрезать, принимает движение, которое является результатом движения качения относительно зубчатого генератора профиля и инструмента инструмента относительно протеза. Таким образом, достигается непрерывное движение, все зубцы режутся позже в том же количестве, что и они соприкасаются с инструментом, и машина останавливается только тогда, когда все зубы полностью обработаны. Машина обеспечивает необходимую ретракцию инструмента для тех частей поверхности, которые не соответствуют граням зубов.
Азотирование - насыщение поверхностного слоя азотом. Обеспечивает особо высокую твердость и износостойкость поверхностных слоев зубьев. Для азотируемых колес обычно применяют молибденовую сталь 38Х2МЮА или стали и 35ХЮА, не содержащие молибдена. Расширяется применение мягкого азотирования, как более производительного процесса с использованием сталей 4ОХ2Ш 40ХФА. В связи с минимальным короблением зубья после азотирования не шлифуют. Поэтому азотирование применяют для колес с внутренними зубьями и других деталей, шлифование которых затруднительно.
Даже в этой машине необходимо было бы отрезать две стороны зубов отдельно, но чтобы ускорить работу, которую они работают, отказавшись от «предельной точности», трех подходящих инструментов, один из которых предназначен для черновой обработки, а два других - при резке двух смежные поверхности. Интересной конструктивной характеристикой машины Рейнекера является то, что инструменты, качающиеся соответственно по режущей кромке, в определенное время занимают наиболее удобное положение резака.
Практически инструмент имеет прямолинейную альтернативу держателю инструмента; держатель инструмента имеет очень медленное вращение вокруг оси неподвижного колеса, соответствующее прокатке примитивной поверхности плоского колеса, к ролику, подлежащему разрезанию, для создания контура; колесо, которое должно быть отрезано, в свою очередь, вращающимся движением непрерывно вокруг к его неподвижной оси, соответствующей движению инструмента относительно плоского колеса, чтобы генерировать поверхность последующих зубов, и катить примитивную поверхность для формирования профиля зуба.
Недостатками азотированных колес являются малая толщина упрочненного слоя (0,2. ..0,5 мм), не позволяющая применять их при ударных нагрузках к опасности растрескивания упрочненного слоя и при работе с интенсивным износом (при загрязненной смазке, попадании пыли) из-за опасности стирания упрочненного слоя и быстрого выхода передачи из строя; длительность и дороговизна этого процесса.
Как правило, поверхность зубов с плоским колесом генерируется инструментом постепенно в другом порядке, чем поверхность, в которой они расположены, чтобы получить удобную форму зубов. Коническим конусом, концептуально отличающимся, является машина Клингенберга. В нем зуб плоского колеса представлен полосатой поверхностью, сечение которой с примитивной плоскостью состоит из проявителя кругового круга; и эта же поверхность получается путем обволакивания режущих кромок усеченного конуса соответствующей усеченной формы, которая вращается вокруг своей оси, в то время как плоское колесо вращается с соответствующей угловой скоростью.
Цианирование -- насыщение поверхностного слоя углеродом и азотом в целях повышения его механических свойств. Цианированный слой имеет малую толщину и сравнительно легко разрушается при ударных нагрузках.
Зубья с твердостью рабочих поверхностей < НВ350 после термообработки допускают чистовое нарезание с высокой точностью. Они хорошо прирабатываются и не подвержены хрупкому разрушению при динамических нагрузках. При твердости?НВ350 нарезание зубьев затруднительно и они плохо прирабатываются. Поэтому их необходимо нарезать до термообработки. Последующая термообработка (особенно объемная закалка, цементация) вызывает значительное коробление зубьев, которое приходится исправлять дорогостоящими операциями - шлифовкой, притиркой, обкаткой и т.п.
Принимая коническое колесо, чтобы вращать вращающееся движение, как если бы он приводился в движение плоским колесом, режущие кромки мельницы разрезали его и генерировали поверхность зубов. Если колесо подвергается термическим процессам, чтобы получить определенные механические свойства материала, из которого он изготовлен, и особенно твердость поверхности зуба, необходимо устранить влияние деформаций, которые изменяют форму зуба. шлифование простейших типов зубных машин есть подходящие машины, которые служат в качестве инструментов абразивных абразивных колес, вращающихся вокруг их оси.
Зубчатые колеса высокой твердости, обеспечивающие малогабаритные передачи с минимальной массой на единицу передаваемой мощности, широко применяют в крупносерийном производстве.
В правильно спроектированной зубчатой паре соотношение твердости рабочих поверхностей зубьев шестерни и колеса не может быть выбрано произвольно.
Для выпрямления цилиндрических зубчатых колес некоторые используют форму шлифовального круга и опираются на один и тот же основной принцип резания зубов с помощью шлифовальных кругов в то время как другие Маагс реализуют принцип резания в каждом поколении, так что Мааг повторяет кинематическую схему подобных друг другу. Вращающееся колесо колеблется, катясь перед зубцами ассортимента, как если бы примитивная поверхность должна была быть проведена, плоская поверхность зуба зуба представленный краем чаши.
Во время хода шлифовальный круг огибает зуб плоского колеса, а также происходит в передачах. В случае цилиндрических и конических зубчатых зубов с общими зубцами ректификация имеет значительные трудности, и тогда мы довольны операцией, которая заключается в том, чтобы управлять двумя моментами пары в аналогичных условиях с теми, которые используются при мокрой ток смазки, который удерживает абразивную пыль в суспензии. Это в некоторых случаях приводит к устранению мелких дефектов и, в целом, тишине крутящего момента во время работы в текущей работе.
Зубья передачи общего машиностроения обычно изготовляют по 6…8-й степени точности. Большое распространение в современном машиностроении имеет эвольвентное зацепление, т.к. она наиболее проста и дешева Это объясняется тем, что эвольвентный профиль зуба состоит из одной кривой без точек перегиба.
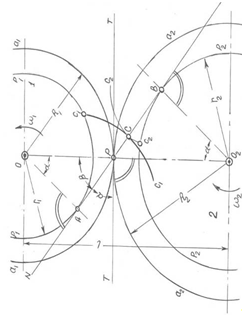
Рис.11. Угол зацепления зубьев
Иногда прямые зубчатые цилиндрические зубчатые колеса после резки и до термообработки подвергаются процессу чистки с целью устранения небольших неровностей из-за того, как инструмент работает во время зацепления зуба. Инструменты, используемые для проверки геометрических характеристик зубчатых колес, учитывая большую точность, требуемую в современных механических конструкциях, становятся все более совершенными.
Некруглые шестерни, несомненно, являются нишевым производством, но есть бесчисленные приложения, которые делают этот тип передач привлекательным. Пара круговых шестерен, т.е. обычных, используемых почти во всех передачах, имеет функцию максимизации передаваемой энергии с постоянным отношением, которое зависит от соотношения между количеством зубьев ведущего колеса и управляемым.
Пользуясь методом Эйлера, проведем через поле зацепления Р (рис.11) под некоторым углом в к линии центров О1РО2 прямую MN и опустим под неё перп-ры О1А и О2В из центров О1и О2 радиусами О1А=r и O2B=r2 опишем основные (производящие) окружности с1 и с2. Выбрав на производящей прямой MN производящую точку С покатим эту прямую MN по основным окружностям с1 и с2 в каком угодно последовательном порядке, например, сначала по окружности с1, а затем по окружности с2. Тогда точка С прямой MN опишет соответствующие эвольвенты c1Cc1 и c2Cc2. Т.к. по известным свойствам эвольвенты прямой MN являются общей нормалью эвольвентою c1Cc1 и c2Cc2 в точке С их касания и проходит через полюс Р зацепления, то эти кривые на основании закона зацепления пригодны для профилей зубьев при перед. числе а именно: эвольвента c1Cc1 даёт профиль зуба колеса I, а эвольвента c2Cc2 профиль зуба колеса 2. Производящие окружности с1 и с2 является основными эволютами, эвольвенты которых дает профили зубьев. Все наглядно видно из рис.12, где сохранены обозначения (Рис.11).
Угол б=90°в между производящей прямой MN и общей касательной ТТ к начальным окружностям в точке их касания Р называется углом зацепления. Из (рис.12) на котором контакт зубьев показан в полюcе зацепления Р как это обычно принято в технических чертежах видно, что профиль зуба состоит только из одной кривой эвольвенты c1Cc1 или c2Cc2.Форма этой кривой определяется радиусом r этой окружности и совершенно не зависит от элементов одного колеса. Это позволяет применять эвольвентное зацепление в сменных передачах, сериях колес.
Радиусы основных окружностей (рис. 11.)
Следовательно
При данном радиусе r основной окружности получим одну и ту же эвольвенту независимо от положения прямой MN касательной к этой окружности, т.е. независимо от угла зацепления б, а также независимо от выбора той точки на производящей прямой MN, которая описывает эвольвенту.
Как известно, эвольвента никогда не может оказаться внутри основной окружности (рис.13). Поэтому, если радиус R? окружности впадин a? больше радиуса r основной окружности (рис.12), то весь профиль зуба (от окружности выступов) полностью будет очерчен по эвольвенте, начинающейся от основной окружности. Если же R? Из построения эвольвенты окружности следует, что все эвольвенты одной и той же основной окружности радиуса одинаковы, независимо от выбора начала эвольвенты в точке 0 или 1 и т.д. Так как любая точка производящей прямой MN, рис.11 при качении последней по соответствующим основным окружностям описывает оба профиля зубьев касающихся в этой точке, то производящая прямая MN проходящая через полюс зацепления Р является геометрическим местом точек касания зубьев, т.е. линией зацепления. Эта прямая или симметрично расположенная прямая MN рис.12 является в то же время общей нормалью касающейся профили зубьев в их точке касания. Рис. 12. Выпуклые профили зубьев
Рис.13. Линия зацепления
Каждое из зацепляющихся колес ограничена снаружи своей окружностью выступов, за пределы которой оно не выходит, поэтому действительная линия зацепления определяется двумя крайними точками K и L рис.13. Угол зацепления на практике колеблется в пределах чаще по ОСТ берут б=20° иногда 15°. При эвольвентном зацеплении (рис.12) направление передаваемого и воспринимаемого усилия на зубья остается постоянным что так и является большим преимуществом этого зацепления. Пробили зубьев при внутреннем зацеплении показаны на рис. 14. эвольвентами С1с1 и С2с2 полученными при качении производящий прямой MN вспомогательным окружностям с1 и с2. Выпуклый профиль С1С2 зуба шестерни работает по вогнутому профилю зуба большого колеса, вследствие чего наряду уменьшения скольжения профилей зубьев, уменьшается износ этих профилей и повышается КПД передачи, срок службы зубьев и плавности работы кроме того, зубья в данном случае получаются более прочными. При внутреннем зацеплении лишь центровое расстояние по формуле получается гораздо меньше, чем при внешнем зацеплении. При внутреннем зацеплении оба колеса вращаются в одном направлении. Внутренне зацепление в последнее время находит широкое применение в редукторах вследствие этих больших преимуществ. Общие положительные качества эвольвентного зацепления: Рис.14. Профили зубьев при внутреннем зацеплении эвольвентами
Сравнительная простота и дешевизна изготовления, возможность применения в любых сочетаниях колес, включая сменные их передачи т.к. профиль зуба одного колеса определяется элементами только этого колеса: постоянное направление передаваемого зубьями. Далее, т.к. кривая, равноотстоящая эвольвенте, есть та же эвольвента, то при эвольвентном зацеплении не требуется особенно точное соблюдение межцентрового расстояния. К недостаткам эвольвентного зацепления надо относить то, что для получения спокойной передачи вращения требуется сравнительно большое число зубьев на шестерне, а это приводит к увеличению габаритов и утяжелению механизма, т.е. удорожанию всей установки. Для уменьшения износа и ослабления зубьев приходится иногда прибегать к исправлению профилей зубьев, что обычно возможно лишь для парных, но не для сменных колес. Остановимся на способе профилирования зубьев по огибающей применяемой тогда, когда профиль зубьев одного колеса задан. Это встречается на практике в трех случаях: 1. Когда одно колесо имеет цевки, т.е. круглые цилиндрические зубья (Рис.15). 2. При ремонте колес, когда взамен сломанного или износившегося колеса надо построить новое при условии правильного зацепления с существующим колесом. З. При проектировании вращающихся поршней для ротативных машин-машин насосов, компрессоров и т.п. Рассмотрим цевочное зацепление (рис.10). Удерживая неподвижный колесо А, профиль зубьев, которого необходимо покатить по нему цевочное колесо А2 и наметим точки этициклоиды Р-а, описываемой при этом центром цевки (рис.10). Затем проводин из центров, взятых на полученной эпициклоиде Р-а произвольно, но на небольшом расстоянии один от другого. Ряд окружностей радиусов равным радиусу r цевки; построим по лекалу огибающую bb1 т.е. кривую, касающуюся начерченных окружностей. Эта кривая и будет требуемым профилем зуба первого колеса A1,впадине его обычно очерчивается полуокружностью радиуса r1, несколько большего, чем радиус r цевки. Как показала практика, изнашивание зубьев будет меньше, когда ведущим является зубчатое колесо, а цевочное - ведомым. По - прежнему шаг зубчатого колеса должен равняться шагу цевочного колеса (рис.15). В последнее время цевочное зацепление вновь широко применяют в виде так называемого внецентроидного эпициклоидального цевочного зацепления. Общий прием построения сопряженного профиля зуба по заданному профилю зуба другого колеса показан на рис.16. Сопряженный профиль m?m? строим графически. Для этого откладываем на начальных окружностях OO и О?О? несколько небольших равных частей: Ра=Ра?, ab=a?b?, bc=b?c? и из точек делений А,в,с... дуги приводим нормали, к заданному профилю имеющегося зуба. Из точек делений а",в",с".. начальной окружности O"о? приводим дуги окружноcтей радиусами aA, bB. cC.Обобщающую к этим дугам кривая и даст искомый профиль зуба второго колеса сопряженный в данным профилем mm зуба существующего колеса. Рис.15. Цевочное зацепление
Рис.16. Построение сопряженного профиля зуба по заданному профилю зуба другого колеса
Недостаток этого способа - неточность проведения нормали. При заданном профиле зуба одного из колес передача вращения на полный оборотив не всегда возможно. При увеличении радиуса одного из зубчатых колес до бесконечности получается зубчатая рейка В (рис.17), а колесо А как имеющее меньший радиус называется шестерней; в этом случае имеем зацепление шестерни и рейки, для рейки начальная прямая ТТ заменяет начальную окружность. При правильной работе механизма шестерни и рейки линейная скорость рейки В должна быть равна окружной скорости шестерни на её начальной окружности радиуса R1, поэтому Для этого механизма при передаче от шестерни А к рейке В передаточное отношение математически iAB=?, а при передаче от рейки В шестерне А передаточное отношение iAB=0 т.к. угловая скорость рейки При эвольвентном зацеплении всегда применяемом в механизме шестерни и рейки, с производящей прямой MN рис.17 получим по прежнему эвольвенту аа для проведения зуба шестерни при качении этой прямой MN по основной окружности с1 радиуса r1. Способы нарезания зубьев зависит от размеров и назначения колес, их скорости и передаваемой мощности, чем определяется необходимая точность обработки рабочих рабочий поверхностей (профилей) зубьев, качества материалов и т.п. Точность обработки профилей зубьев может колебаться в пределах от I до 4 -классов, но чаще от 2-х до 3 классов. Современные методы нарезания зубьев можно разделить на две различные группы: Метод скопирования и метод обкатывания. Метод копирования (деления) можно разделить на след. два способа: а) нарезание зубьев фасонным инструментом самых разнообразных типов, причем профиль инструмента в точности соответствует требуемому профилю промежутка (впадины) между зубьями нарезаемого колеса (рис.18 и рис.19.). б)нарезание зубьев простым резцом, воспроизводящим профиль промежутка между зубьями при определенном движении резца например, направляемого соответственным шаблоном. Фасонные инструмент-., по профилю соответствующие промежутку между зубьями, могут быть в виде дисковой фрезы В рис.18 или в виде пальцевой фрезы (рис.19). Нарезанные по методу копирования зубчатые колеса работают удовлетворительно лишь при небольших окружных скоростях не свыше 4-5 м/сек. При обкатывании можно различать три способа нарезания зубьев при внешнем эвольвентном зацеплении: а) первичный фрезой 9 рис.19). б) режущий шестерней, или долбяком В (рис.18). в) режущий рейкой или гребенкой. При внутреннем зацеплении по методу обкатывания можно нарезать зубья лишь долбяком (Рис18). Закругление ножки Рис.17. Зацепления шестерни и рейки
Рис. 18. Способ нарезания зубьев: 1) дисковый фасонной фрезой; 2) долбяком; 3) накаткой
Рис.19. Нарезание зубьев: 1) пальцевой фрезой, 2) модульная фреза зуба у основания получается при нарезании автоматически
Способ нарезания зубьев дисковой фасонной фрезой показан на (Рис.18), где А нарезаемая в виде отливки или поковки обточенный снаружи по радиусу R? окружности выступов и по объемам торцевым плоскостям, а также расточенный в центре вала но еще без зубков. Вследствие дороговизны фасонных фрез часто довольствуются набором из восьми фрез для каждого модуля при нарезании колес всех размеров, начиная с Z=12 и кончая рейкой Z=? поэтому каждую фрезу заменяют при определенных числах зубьев а именно: При этом получается некоторая неточность профиля зубьев и чтобы уменьшить эту погрешность, то пользуются более широким набором из 15 или 26 фрез для каждого модуля. Старейший способ нарезания зубьев по методу обкатывания на зубофрезерных станках - применение червячной фрезы, имеющие в общем вид червяка, но с продольными прорезами для выхода стружки и с задней заточкой, каждый виток образует ряд режущих лезвий, как это видно на чертеже. При нарезании зубьев и заготовке и фреза вращаются; одному обороту однозаходной червячной фрезы соответствует поворот заготовки на величину шага t зацепления на начальной окружности нарезаемого колеса. Ось фрезы устанавливается под соответственным углом к оси заготовки, а подача производится вдоль оси заготовки, поэтому все зубья нарезаются одновременно по всей окружности, но постепенно по длине зуба; холостой ход здесь совершенно отсутствует, вследствие чего метод нарезания зубьев червячной фрезой, отличается большой производительностью. Недостаток этого способа - значительная дороговизна червячной фрезы. Позднее был предложен другой способ нарезания зубьев по методу обкатывания на зубодолбежных станках, основанной на применении более простой и дешевой режущей шестерни, или долбяка (Рис.18.). Рабочий ход долбяка В происходит на стрелке I вниз, как в долбяжных станках холостой ход долбяка происходит снизу вверх. Перед каждым новым ходом долбяк в и заготовка А вращаются по стрелкам 2 и 3 для снятия новой стружки. Зубья нарезаются один за другим. Этот способ - единственно пригодный для нарезания зубьев колес с внутренним зацеплением по методу обкатывания; он применим для нарезания прямых, косых шевронных зубьев. Наиболее новым способом нарезания зубьев по методу обкатывания является применение в зубострогальных станках режущей рейки, или гребенки, являющейся заменяй круглого режущего колеса (долбяка) прямолинейной рейкой, соответствующей режущему колесу с числом зубьев Z=?. Это наиболее простой дешевый и точный режущий инструмент. Кроме цилиндрической червячной фрезы рис.19. часто применяют коническую фрезу с добавочным движением вдоль её оси, такую же Фрезу применяют для нарезания прямолинейных зубьев на конических колесах. В современном машиностроении при требуемой практикой точность обработки быстроходных и мощных зубчатых передач, большое значение имеет доводка зубьев, т.е. сообщение им наибольшей точности профиля и шага, а также наибольшей гладкости и твердости рабочих поверхностей зуба. К таким процессам относятся процессы шевингования, шлифования и притирки. Использование зубачатой шестеренки и рейки - частный случай зубчатой передачи, широко используемой в станках и механизмах для передачи вращательного движения и преобразования угловых скоростей и крутящего момента. Зубчатые шестерни выполняются с прямыми зубьями для работ на малых и средних скоростях, с косыми зубьями для использования на средних и высоких скоростях или когда требуется повышенная точность перемещения. Передачи c использованием зубчатой рейки получили широкое распространение в машиностроении благодаря удачному сочетанию нагрузочных, динамических и точностных характеристик. Они отличаются надежностью, простотой конструкции и удобством монтажа. Мы предлагаем зубчатые шестеренки с модульным шагом: M1, M1.5, M2, M2.5, M3, M4, M5, M6, M10. В качестве дополнительных элементов трансмиссии используют зубчатые колеса конических передач, изготовленных из стали C45 UNI 7845. Все поставляемые компоненты отличаются традиционно высоким европейским уровнем исполнения. Прецизионные шлифованные конические пары подбираются индивидуально и проходят тщательную подгонку. Высокоточные конические шестерни со спиральными (паллоидными) зубьями выдерживают несколько этапов шлифовки и финишной притирки. Этот тип шестеренок разделяются на несколько видов, различающиеся по форме линии зуба. Подобрать такую шестеренку, которая подойдет именно Вам, помогут расположенные в категориях фильтры. Для удобства выбора можно отсортировать по следующим параметрам: В каждой карточке товара есть чертеж с размерами и характеристиками. Если Вы затрудняетесь в выборе, воспользуйтесь любым (e-mail, телефон, форма обратной связи) способом задать вопрос нашим консультантам и мы с удовольствием поможем Вам найти шестеренку с необходимыми габаритами.
Коническая зубчатая передача